PACIFIC MAKO FOUNDRY
For Over 75 Years We've Provided Aluminum Casting
Solutions For A Variety Of Applications
We Have Decades Of Experience In Managing The Entire Spectrum
Of Production Services For Our
Clients
Our Facility Is Equipped To Make Consistent Molds Accurately
- Forestry
- Oil & Gas
- Mining
- Marine
- Transportation
- Heavy Equipment
We've Produced Aluminum Casting Components For Various Industries
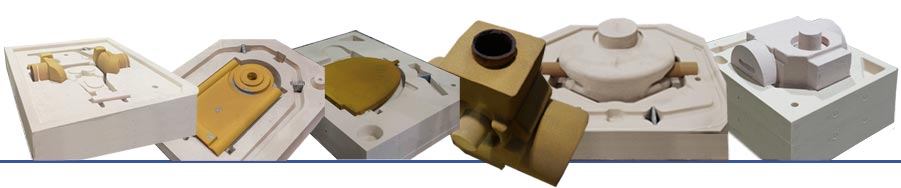
OUR VALUES & PHILOSOPHY
- Our Company:
- ... is dedicated to providing solutions for all of our clients.
- ... enjoys providing design suggestions.
- ... takes on challenging and complex casting applications.
- ... is always professional and friendly.
- ... offers reliable service.
- ... is dedicated to continuous improvement.